Of all the boxes that will be shipped this holiday season, this one stands out
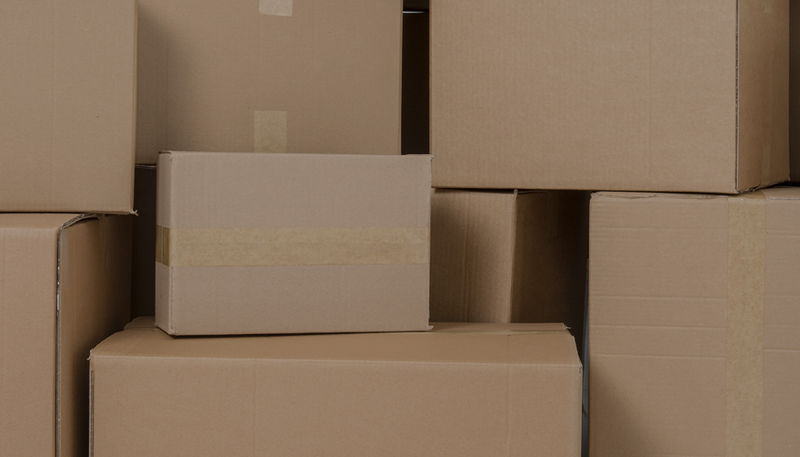
The story of the first Covid-19 vaccines reaching frontline healthcare workers is a triumph of human ingenuity on every conceivable level, a huge bright spot at the end of a very challenging year. In this USA Today item Gen. Gustave Perna, co-leader of Operation Warp Speed in charge of logistics, is quoted comparing it to D-Day in World War II, “a pivotal turning point” and “the beginning of the end," of the global pandemic.
Would you be surprised to hear, though, that my favorite part of the story comes a bit later?
“It was being packaged Saturday at the Pfizer manufacturing site in Portage, Michigan just outside of Kalamazoo. On Sunday the packages will begin the journey to distribution hubs to be shipped by UPS and FedEx, Perna said.
"Right now, boxes are being packed and loaded with vaccine with an emphasis on quality control," he said.
That involves Pfizer personnel taking five-dose glass vials of vaccine out of subzero freezers and packing them into the company's specially designed shipping container, Wes Wheeler, president of Global Healthcare at UPS, told USA TODAY.
Each vaccine shipping box weighs about 80 pounds and holds up to 4,875 doses of vaccine. There are five doses per vial. The vials are packed in flat boxes about the size of a small pizza box, each of which holds 195 vials. As many as five of these are stacked together in a reusable, insulated cardboard box that is topped with 50 pounds of dry ice.
Pfizer is also sending facilities special instructions for handling the custom packaging, designed and manufactured by Softbox, in order to preserve the precious cargo.
Everyone I’ve talked to in our industry is just so proud and so excited that at the center of this effort is the (extra)ordinary corrugated cardboard box—lightweight, strong, moisture resistant, insulating—the perfect material for the most important packaging and shipping jobs in the medical and pharmaceutical worlds. Even better, 100 percent of the packaging is recyclable, personally collected by the manufacturer’s in-house recycling service and sent to partners in other industries to make a variety of new products.
One of the threads running through the Paper and Packaging Board from its very early days—when it was just a few of us brainstorming in conference rooms—is that paper-based packaging is technology. Yes, it’s also a commodity, and a convenience, and a staple that is so ubiquitous in our lives that is can sometimes just fade into the background. But every bit as much as a smartphone or a tablet, it’s also an engineering marvel. A bona fide gadget that is being innovated every day to do new, wondrous things.
We tried to bring this engineering marvel corrugated to life in our mini-doc on the packaging testing and design lab WestPak.
One of the areas of the lab that didn’t make it into the video was its series of sealed, temperature-controlled chambers used to subject packaging to extremes of heat, cold, and humidity for hours, day, or weeks, to test how different material stands up to every shipping environment imaginable. Obviously, a bunch of boxes sitting in a sealed room doesn’t make for the most exciting footage! But it was one of the quiet revolutions in temperature-controlled packaging, storage, and shipping that play such a crucial role in this moment of hope and promise.